SERIES
Bend series
Tee series
Flange series
Reducer series
Simmer the bent pipe ser
Wear-resistant pipe fi
Plant accessories series
Ripple compensator seri
Pipe expander
Cleaner series
Piping support series
Head cap
Pipe series
Insulation series
Series of anti-corrosion
Concrete pump accessories seri
Plastic Lined Pipe Series
Surfacing machine / wire drawi
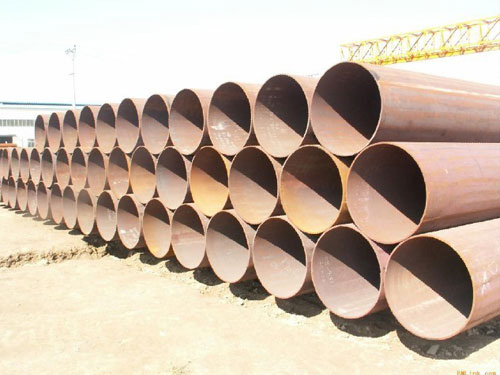
Make a straight pipe
The pipe is made of steel plate as raw material, and after different molding process, the welding tube is made with double - face submerged arc welding and welding rear diameter. Straight seam submerged arc welding pipe production process either production methods, such as ultrasound edge, edge milling, processing and steel spot welding, both inside and outside the tube after forming buried solitary welding, ultrasonic flaw detection, hole diameter and water pressure test tube is basically the same, the key is different forming processes. Therefore, according to the forming process, SAWL can be divided into four types: roll bending forming (building strength), continuous torsion forming, UOE forming and JCOE molding process.
RBE forming is a traditional molding process. The forming method is to make a cylinder of the steel plate after pressing the edge of the steel plate, and then use the double-sided submerged arc welding to form the cylinder. The forming method has the advantage of small equipment, light weight, less investment, wider range of pipe diameter, output and moderate production flexibility, strong adaptability to the market, but there is also a pipe barrel open big, easy to mistake the shortcomings such as edge, not easy to control. For large diameter, high grade, large wall thickness steel production is difficult, because of lack of support in central on the molding in shaping roller, restricted by its stiffness, wide tend to appear in the middle, two narrow phenomenon.
The continuous torsion forming process adopts the core rod torsion forming process, which is used to process the smooth steel plate through a vertical clamp clamping and three rolls of rolled plate, which is processed into a long segment of the cylindrical tube. The roll forming machine consists of three rolls, the upper roller is the forming roller, the longitudinal clamp is fixed, and the diameter of the roller must be changed according to the production specification. The lower roll is two driven rollers with a certain diameter and fixed position. It is not changed with the specification of the steel tube, and it has the function of limit, fixing and support. The continuous torsion production line is characterized by the quick and simple change of the specifications, the flexibility of variety, the wide range of product specifications, and the size of any diameter in the production specification. But in the production of different combination of steel pipe diameter and wall thickness size, need a lot of forming core roller, cost is larger, and the welded pipe forming precision of small diameter, large length is poorer, prevent partial device not effectively control the quality of contact point.
The production process of the straight pipe and steel pipe is explained by:
1. Board: after the steel plate enters the production line, the whole plate ultrasonic inspection shall be carried out first.
2. Milling edge: the edge milling machine is double-sided milling on the edge of the steel plate to achieve the required plate width, edge parallelism and the shape of the groove and the pre-filling process of the double submerged arc welding;
3. Precurving side: also known as the 10,000 ton hydraulic press, the German equipment is adopted. The bending machine is used to prebend the edge of the plate to meet the required curvature.
4, molding, molding machine on the first half of the steel plate after bending after many step punching, pressing "J" type first, and the other half of the steel plate bending, same pressed into C "type", form open O "type. At this point J CO pressure is basically forming.
5. Pre-welding: weld steel pipe with straight seam after molding and gas shielded welding (MAG) for continuous welding; Make steel pipe close molding
6. Internal welding: the welding of the inner side of the vertical seam pipe is used for the welding of the double submerged arc welding.
7. External welding: the welding on the outside of the welded steel tube of the straight seam arc welding is performed by the longitudinal column multi-wire submerged arc welding.
8, ultrasonic inspection Ⅰ: inside and outside of straight seam welded steel pipe weld and weld on both sides of the base of 100% of the check;
9, X-ray inspection Ⅰ: 100% of inside and outside weld X-ray industrial TV inspection, using image processing system to ensure the sensitivity of detection;
10. Expanding diameter: the diameter of the steel tube was expanded to improve the accuracy of vertical and roundness of the steel tube, and the distribution of the internal stress of the steel tube was eliminated;
11. Water pressure test: the test pressure to ensure the steel pipe to meet the standard requirements is carried out by root test on the steel tube of the water pressure test machine to ensure that the steel pipe meets the standard requirements; the machine has automatic recording and storage function;
12. Chamfering: the pipe end shall be processed after the qualified steel pipe is inspected to achieve the required size of the pipe end groove;
13, ultrasonic inspection Ⅱ: root by ultrasonic inspection to check again after the straight seam welded steel pipe in the hole diameter, water pressure may produce defects;
14, X-ray inspection Ⅱ: after the hole diameter and water pressure test of steel pipe detection of X-ray for the second time.
15. Tube end magnetic particle inspection: carry out this inspection to find out the pipe end defects;
16. Anti-corrosion and coating: the qualified steel pipe shall be corrosion-resistant and coated according to the user's requirements.